Aptean Distribution ERP, SWORDS Edition - Voice Directed Warehouse Management System for Wholesalers
Aptean Distribution ERP, SWORDS Edition - Voice Directed Warehouse Management System for Wholesalers
Aptean Distribution ERP, SWORDS Edition - Voice Directed Warehouse Management System for Wholesalers
6 Jul 2020
Aptean Staff WriterHeadline
- Dramatically Reduce Picking Errors and Increase Warehouse Productivity
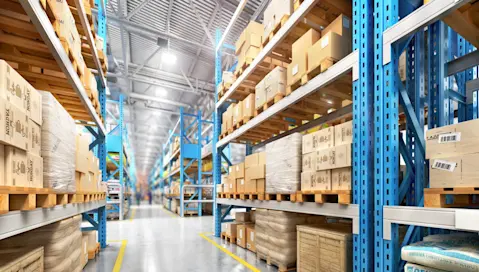
Your staff can increase efficiency, improve productivity and save costs with our voice directed Warehouse Management System (WMS).
The solution benefits both the picker and your business by boosting the efficiency of your order picking operations. It uses speech recognition for accurate hands-free order picking and intelligent routing to save time and increase the number of orders picked.
Voice directed order picking software sends picking instructions to warehouse operatives via a wireless headset and microphone. Pickers communicate with the system by providing answers to structured questions, quickly identifying stock and picking the stock orders as required. With hands-free picking, your staff can increase efficiency, improve productivity and reduce handling damage costs.
More Accurate Picking and Less Costly Errors
Orders are picked accurately based on verbal commands, reducing the costs associated with processing refunds and collecting and returning goods.
Increased Productivity With Faster Order Picking
With no need to carry handheld devices or return to work stations to collect the next pick list, pickers can benefit from easier, more streamlined picking.
Training Is Easy and Fast
The system is quick and simple to use, reducing your training costs. It is intuitive and user-friendly. With a fast familiarisation session, the picker can start picking almost immediately. This is beneficial in operations where there is heavy use of temporary staff.
Real-time stock information
Manages and monitors real-time stock movements for added accuracy and peace of mind.
Enable Faster and Easier Picking
Voice directed WMS offers:
Fewer costly picking errors, reducing the costs of processing returns and increasing customer satisfaction
Reduced administration compared to printed pick list processes
Continual picking with no need to return to work stations to collect the next order
Hands-free picking to increase productivity, especially in chilled warehouses or other environments where gloves are required
Simple and easy use which reduces training costs
If you are looking to boost warehouse productivity and increase picking accuracy, contact us to chat with one of our experts or schedule a demo to find out more about how Aptean Distribution ERP SWORDS Edition can help your business.
Related Content
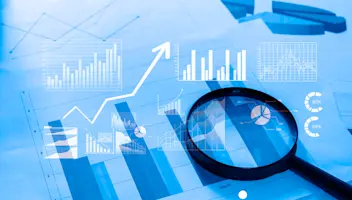
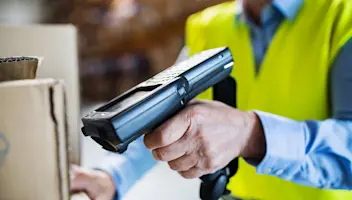

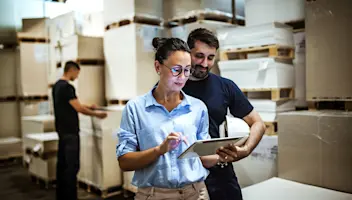
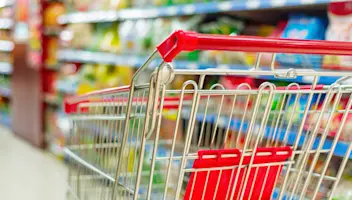
Start transforming your distribution operation
If you’re ready to take your business to the next level, we’d love to help.
